Contents:
- Performance Brake Discs.
- Brake Pads.
- Brake Lines.
- Brake Cooling and Ducting.
A brake disc can be made of a number of different materials including castor iron, ceramics and composites (including Carbon, Kevlar and Silica)- as you can imagine the more exotic the materials, the higher the price tag. These materials use are an attempt to reduce brake fade, increase heat dissipation and the cars overall stopping power. While not all materials will be safe or effective for the road due to usage criteria, careful selection should be taken as mentioned previously. The disc (rotor) can also have different designs including drilled, crossed and drilled and cross design. Ultimately performance brakes are trying to convert the kinetic energy to heat as effectively as possible and deal with repetitive use- holes or slots in the disc (rotor) are primarily a heat management design function- to help address this issues.
Jackie Stewart from F1 once said that the last thing a Racing Driver learns to do properly is a brake, yet the ability to race and to overtake another racer has a lot to do with being able to brake really effectively.
Performance Brake Discs:-
When you increase the engine power, more and more development work will be required to the braking system to help harness that extra power potential on the track or road. This could include fitting bigger discs (rotors) and possibly uprated to lighter brake callipers. This is one of the easiest ways to get serious performance gains over standard equipment. You might have to bear in mind what performance levels your starting with and available Budget.
Not only will the uprated callipers increase braking efficiency, but they will also help achieve better cooling for the braking system. More cooling efficiency equals better braking performance. But another effect will also be to reduce the vehicle mass and even the unsprung weight of the suspension system. This will slightly increase cornering and acceleration abilities along with the desired braking increase performance.
If you are on a budget or going to undertake some of the work yourself and if you are starting with a standard road car. Why not look at the more powerful models in the range, for suitable performance donors if you're not already driving a top of the range model. If you look at the VW group, for example, you will see many parts and components are easily interchangeable. Sometimes with little or minimal modification needed.
Some professional braking systems can cost a small fortune and if you have that sort of money, your most likely will have your own mechanic and maybe race engineers, along with that corporate sponsorship deal. Well, there is always wishful thinking.
DRILLED BRAKE DISCS :-
Drilled brake discs are viewed as a good performance brake upgrade compared to standard OEM equipment supplied with many of today's cars. In the world of profits and service revenues for manufacturers, performance is viewed as a premium and normally reserved for the flagship or performance models. Making it quite rare to see on stock applications- do not go thinking that these are simply normal disc/ rotors with holes in, as you can notice that ventilation on the rim of the disc/ rotor is present. Also, some designs are not actually holes but dimples as such not going through the whole disc surface.
Fitted as standard equipment on many high-performance machines though, this brake design has a number of key advantages compared to standard components and have been used in Rally and Racing for some time now. Bear in mind that any braking upgrade should be looked at as a whole and it would be unwise to just fit uprated discs without looking at other components as well.
DRILLED BRAKE DISC ADVANTAGES:
- The added holes or dimples allow for better cooling of the disc, by drawing more air into the internal vanes to lower temperatures- depending on the design- ultimately increasing heat dissipation.
- The edges of the holes clean pad surfaces to a degree, also provide increased braking bite on pedal application. Also increased brake pad friction materials can be used to enhance braking efficiency- depending on the desired goals of the application.
- The added holes prevent gasses or water from collecting between the pad and disc surface, also in wet weather performance is increased due to less surface water building up with this design.
- The holes reduce the weight of the disk, and therefore its inertia and the unsprung weight is decreased.\
CROSS SLOTTED DISCS.
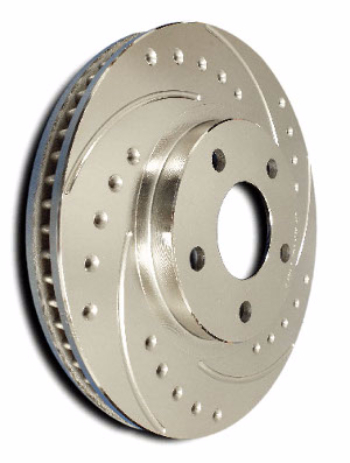
Cross slotted disc/ rotors are quite similar in their goals of trying to increase the initial bite on first brake application of the brake pedal, compared with drilled brake disc.
Benefits also include the removal of gas, dirt, water and debris from the discs. While also maintaining parallel pad wear throughout the disc/ rotor surface, compared to drilled designs alone. This is one of the biggest advantage of cross slotted discs, rather than allowing ridges to develop on pads and discs, which could transmit through the steering and create judder under heavy brake applications.Useful for the longevity of the braking system and resulting in less preventative maintenance.
By preventing these ridges on the disc/ rotor, brakes stay more consistent throughout the lifespan of the component. Also cracking is not normally an issue and this is more suited to endurance application due to this very fact alone.
Again we can this that the sides of the design incorporate vents to help dissipate heat and increase the braking efficiency compared to standard designs.
CROSS SLOTTED AND DRILLED DISCS.
The extra benefits of a drilled and cross slotted discs/rotors configuration include the effects of the slots having on maintaining a flat smooth pad surface during the pads wear life. This helps to eliminate uneven disc wear, especially under full breaking capacity applications.
You could look at this design to be a good comprise of drilled and cross slotted brake designs, taking equal advantages from both and seems to be the best for fast road and race applications.
The slots encourage the pads to wear with a more flat pattern and the "Ribbing", common with non slotted discs doesn't occur here. This normally removes the "Record groove" effect of pads on standard plain discs. Particularly around the outer edge and also helps the pads to maintain better contact area with the disc throughout its lifespan.
There is a good selection of discs to choose from and normally the purpose and the budget will determine the final purchasing decision- but we must stress again to see this upgrade holistically and not as a single upgrade solution, best results will include pad selections, brake lines, callipers and even brake fluids in the overall solution.
Brake Pads.
After upgrading the braking discs/rotors, the next logical step will be to look at the brake pads; we need to identify what the pads are going to be used for and what type of strains and stresses they must undertake. This is one of the easiest car brake upgrades available as it is the material of the pads we are upgrading and no reconfiguration is normally needed.
There is a huge difference in the optimum operating temperature of performance brake pads depending on the material used. For example, cars competing on a short hill climb or low lap races will want the pad to be effective from cold straight away (this is ideal for fast road use also). While others competing in endurance races will most likely have wear rates and longevity as their top priority and brake pad materials may take a few laps to get up to maximum operating temperatures.
When completing in Motorsport disciplines where the braking system has more prolonged use and with higher operating temperatures. Having a pad which is better suited to these higher temperatures and with the main focus to reduce brake fade over long repeated use, this is the key to the brake pads objective. There are multiple different applications, so a well thought out plan is required and its horses for courses with so many other upgrade paths.
As with all car upgrades it is best to ask the expert manufactures for their advice on the exact component match for your goals and needs for your chosen model and application.
Another point to bear in mind is that new brake pads will need a bedding in the process to help get rid of the volatile chemical's normally coated on new pads outer surface. This is just the same for standard OEM pads in roads cars, extreme braking during this period, will most likely cause damage to pads and discs and create uneven wear going forward.
The bedding in the process involved is the gentle application of the brake pedal to bring the pads up to working temperature and then cooling down. In everyday driving, it is advised that no harsh or strong braking application is applied in the beginning, as this could score the disc/ rotor and cause uneven braking in the future life of the pad. Due to the design of the pad, until the outer coating is removed, the pad will not work at optimum braking performance levels.
Brake Lines.
Another often overlooked area is the flexible Brake lines located right near the callipers, these when old are prone to ballooning as they are normally made of rubber- which is affected by its environment. Over time rubber can become brittle and weak, can deform over repetitive use and be a weak point in the system.
When these rubber lines are in sub-prime condition, they could effectively be pumping up and ballooning rather than supply force to the calibres in order to clamp the disc/rotors. This will again yield a spongy feel to the pedal with dented performance levels.
If your going to spend any money on the braking system, then these should be a good investment for any future upgrades and increase the endurance and strength of the system- especially under heavy use.
Upgraded brakes lines can come with replacement steel-braided-outers and Teflon-inner construction design- yielding a good progressive feel to the pedal (especially in term of reliability). The possible ballooning effect with standard lines and the ability to retain their structural rigidity under loads is greatly enhanced. Also if combined with other performance brake upgrades, we further augment heat management, due to the heat shielding properties of the updated components.
These will not only look professional and last longer than standard equipment but are reasonably priced compared to some of the other brake upgrades out there.
Brake Cooling and Ducting.
cover air cooling and ducting for braking systems- as this is very often overlooked, especially after performance upgrades have been implemented. Normally in general car and racecar design, this is factored into the equation from the very beginning, but if your upgrading and modifying existing braking systems then we need to consider the available options to get the best from the new performance level. This section will be with closed wheel racers in mind.
Brake efficiency and maximum performance are not always factored in normal production models design and some work may need to be done on making sure we are supplying enough airflow. The current design limitations in stock could have a negative impact on racing applications and need overhauling.
A braking system is basically a way to convert Kinetic (movement) energy into heat and friction to slow down the car's mass. During this process, heat is transferred or dissipated into the air, similar to air cooled engines or radiators in theory.
By improving the performance braking capacity of a car, it is logical to think with greater stopping power comes greater heat levels. Having a good feed of cold air directed to the braking system and vented in an even fashion- not to cause an in balance of either side of the disc/rotor will greatly increase the performance efficiency. Imbalances could cause temperature fluctuation to crack or damage the braking system in extreme cases. So we need to feed air to the brakes and also away from them in order to reap the best results for consistency.
It is also worth considering the impact on wheel arches and aerodynamic efficiencies, so careful venting needs to be factored into the equation for a complete system. Creating an unwanted drag penalty may not be too much of a problem on a road car, but is an unwanted attribute we can easily design around with a little planning.
Ducting or specially designed tubing runs from the front of the vehicle (normally in the bumper) to the wheel arches and can be an effective way of helping to solve the supply of cold air issue. It will work in a similar way to a cold air feed on an induction system and uses materials which help to shield heat from the supply flow. RAM Air effect uses low pressure fast moving air, to channelled through the vents via ducting and delivers airflow at a faster rate than ambient air can deliver.
We can also have a mirrored effect past the braking systems in order to help dissipate the hot air and help with heat management- once the air supply has done its job. This can again take the form of ducting or tubing and slits or louvres as an exit point- in the bodywork.
Racecar designs have even used air from the radiator ducted to the wheel arches, in a bid to help cool the braking system, with compact and space limited applications.
Active braking vents are an area of development in road cars now, which would be closed during normal driving conditions and activate under braking loads. This has a better effect on the overall aerodynamic package as well by minimising drag when not needed. This could be even be taken further, with vents actually causing lots of drag penalties under braking loads, a sort of air-brake duel use with venting and ducting.